ITM 2012
2012-03-27
Oerlikon with groundbreaking new product developments at ITM
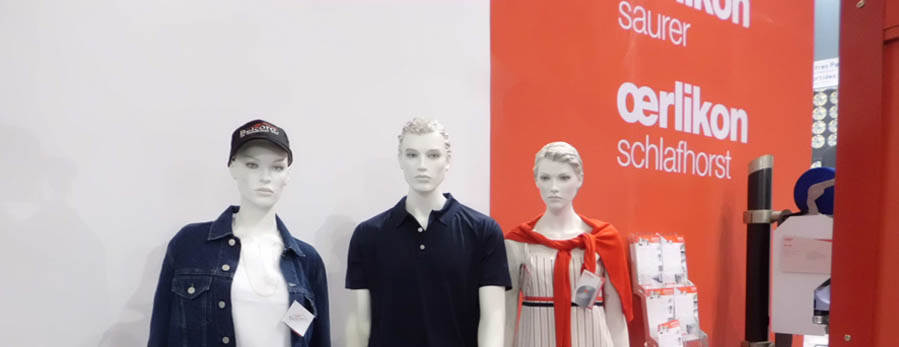
(c) 2012 Oerlikon
Innovation is the key to sustainable success and continual further development while conserving resources. Oerlikon Textile (Hall 2, Booth B210) has mastered this challenge once more.
At this year's exhibition the company is looking forward to present their visitors a series of groundbreaking new product and service developments on a surface of 400 m² at booth B210 in hall 2. Oerlikon Barmag: Texturing and spinning of high-end filamentsThe market leader for filament systems is exhibiting its twelve-thread WINGS for polyamide 6 for the first time and setting new standards in processing the demanding polymer to produce good yarn grades. To prevail against the strong competition from China and India, Turkish filament yarn manufacturers are focusing increasingly on high-quality yarns for the carpet and automotive sectors. One information highlight for the traditionally strong Turkish texturing market is the ITMA innovation eAFK, an automatic texturing machine, along with its manual sibling eFK. The market leader for artificial turf filament systems is also showing its latest development for artificial sports turf: MoisTurf is the name of the equipment for producing hydrophilic monofilaments. Such yarns are used as artificial turf preferably in contact sports and ensure that water is distributed evenly and almost naturally on the yarn surface.Oerlikon Neumag: Superior competence in BCF carpet yarns, staple fibres and nonwoven productionWith a market share of nearly 70 per cent, the company is a leading supplier of highly advanced BCF carpet yarn machines. The BCF best seller in 2011, the S+ with three ends per position, is now available for the up-and-coming raw material polyester. The BCF S+ for polyester is a perfect substitute for polyester spun yarn on account of its cost efficiency in production. Production systems for polyester staple fibres permit maximum capacities of up to 300 tonnes per day and cut operating costs at the same time. For manufacturers of nonwovens such as geotextiles, compact inline systems with capacities of up to 80 tonnes per day offer suitable solutions as they permit small production batches and require few operators. Also on the agenda are machines or turnkey systems for the production of nonwovens from spunbond and meltblown to airlaid. Visitors to the exhibition can also navigate through the innovations in 3D on a virtual tour of the installation.Oerlikon Schlafhorst: One-stop innovations in spinning and winding The market and innovation leader in ring and rotor spinning and winding supplies spinning mills worldwide with innovations for the optimum in quality, reliability and economic benefit. The new Autocoro 8 is thus the first and only rotor spinning machine to spin a yarn at a rotor speed of 200,000 rpm. The new technology forms the basis for productivity increases of up to 25 per cent, machine start-up in minutes instead of hours, an excellent multi-lot capability and much lower spinning costs. The BD 448 is the longest semi-automatic rotor spinning machine in the world. The Zinser ring spinning machines 351 and 451 promise unique process reliability with the Impact FX compact spinning technology and the CoWeMat doffer. And the quality package of the Autoconer X5 sets the benchmark for individually and flexibly adaptable package quality with maximum productivity. Oerlikon Saurer: Embroider and twist perfectly and economize on costsThe market leader in embroidery and twisting is putting the emphasis on energy saving with the new Volkmann CT: the eco-drive concept and spindles are the perfect complement to the e-save spindle family and help to save up to 40 per cent of energy costs, even for the finest yarn counts. Next new process: Volkmann Heat-SET integrates cabling, thermofixing and winding in one process sequence, thus reducing process costs and speeding up order completion. The new Allma TC2 two-for-one twisting machine can process every conceivable material in the titre range from 235 to 60,000 dtex. It thus satisfies the demand for top quality, application variety and production flexibility in the market for technical plied yarns. Its sister machine Allma CC4 is revolutionizing the tyre cord cabling market with energy savings of up to 50 per cent. And the Epoca 6 with its new drive system, optimal adjustment options and perfect thread cutting delivers the product up to 30 per cent faster with maximum reliability and embroidery quality.Oerlikon Textile Components: The best place to go for all premium componentsAs market leader, Oerlikon Textile Components is a byword for quality and know-how in the production of premium components for the filament and staple fibre spinning mill and is exhibiting all ITMA innovations. Special exhibition highlights: in staple fibre spinning, the world’s most versatile Texparts® PK 2630 SE weighting arms can also be used for machines from Rieter and LMW. Spindles with the Texparts® Zero underwinding system prevent underwind threads and offer maximum reliability, efficiency and operator-friendliness in use. The novel curved edge of the Daytex® Shrinkage Belt is completely devoid of sharp edges, preventing tears from forming and thus extending the belt’s service life. The established product lines Accotex, Fibrevision, Heberlein and Temco complete this selection.
Related News
Latest News ITM 2012
2012-07-20
2012-05-09
More News from Oerlikon Textile GmbH & Co. KG
2025-03-13
2025-03-06
Latest News
2025-07-03