ITMA 2015
Moisture: A key factor in sustainable manufacturing
“Over-dry material creates static problems,” says Jim Herbison, Managing Director of Streat Instruments. “It can also reduce fibre strength, resulting in excess fibre breakage, increased drop out and reduced yields. On the other hand, a product that is too wet blocks fibre transports, causes roller laps and can lead to the build up of bacteria.”
Streat Instruments moisture systems are designed to assist users in optimising production conditions in order to maximise productivity, quality, operating efficiencies and profitability in the nonwovens and textiles industries. Over the last three decades he New Zealand-based company has earned international recognition as a premier manufacturer and supplier of moisture management technology.
New App increases control and flexibility
DSC00759Streat will showcase its latest moisture control systems at ITMA 2015. The new Drycom Connect combines well proven Streat control technology with a dedicated smart-phone and tablet app, which allows operators to view moisture and associated production data from their production plants in real time, at any time, from anywhere.
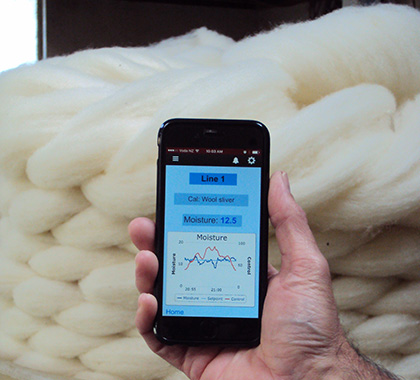
“The Drycom Connect App is a valuable management tool, empowering users to monitor system data remotely,” says Herbison. “Having a mobile option provides an increased level of control as well as peace of mind.”
The App can keep track of multiple systems within the plant and can be integrated with data from fibre weight control systems by Streat’s sister company Garnett Controls.
Sustaining quality with minimal energy consumption
Drying is one of the most energy intensive operations in textile mills. Streat Drycom empowers processors to reduce energy usage by optimising the drying process.
Drycom ensures consistent moisture by continuously measuring the moisture of the fibre, yarn, nonwoven web, or other product outputs at the exit of the dryer.
“Drycom automatically controls the energy and/or speed of the dryer to maintain the desired level of moisture,” adds Herbison. “In addition to ensuring consistent moisture content, the productivity gains and energy savings provided by our systems are considerable.”
Hundreds of Streat Drycom systems are already providing users in over 40 countries with the tools they need to operate sustainably, optimise production processes and maximise productivity, quality, operating efficiencies and profitability.
In processing areas such as opening and blending, carding, and web forming, plant humidity control is not enough to ensure optimum moisture conditions. Micro-climates within machinery often dry the fibre, making downstream processing difficult or impossible. It’s not uncommon for plants to run at high humidity levels (up to 70+ % RH) in order to drive fibre moisture content up to manageable processing levels. High humidity creates an uncomfortable environment for workers, high energy costs, and potential machinery damage.
Drycom measures the fibre directly. Moisture can them be managed in a manner appropriate to the process, such as targeted moisture application by precision spraying devices. Experience in all types of natural and man-made fibres has enabled Streat to build a portfolio of application-specific technologies to ensure sustainable production.