Dyeing, Drying, Finishing
First Thies 4-chamber “iMaster H2O” dyeing unit to Germany’s Carl Meiser
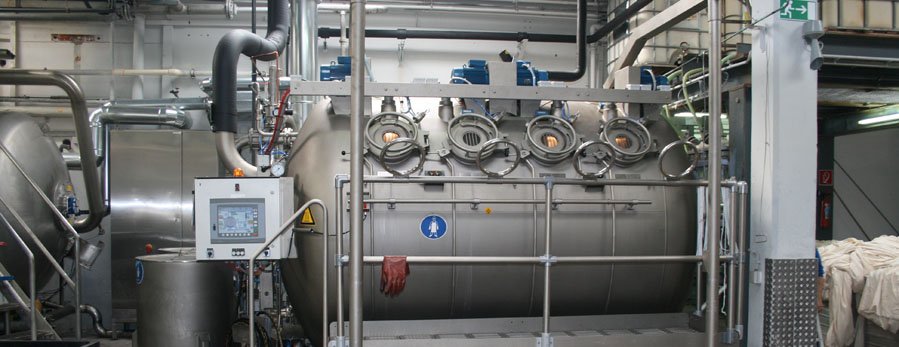
Founded in 1965, Germany’s Carl Meiser GmbH continues to enjoy an enviable reputation as a ‘top of the range’ high quality commission dyeing specialist for modern fabrics and technical textiles under third generation family ownership of CEO, Jens Meiser.
Today with two operating companies – one, Meiser know how in Textiles, a 100% service company, produce dyehouse, bleaching and finishing for ‘top-edge’ ladies, men’s and children’s lingerie and underwear. The second, Nopma Technical Textiles, according to Jens, is a ‘one-stop-shop’ partner for company’s seeking to develop and produce solutions with technical textiles for the aviation, automotive, medical and caravanning sectors.Nopma Technical Textiles, was formed in 1999 capitalising on the Meiser ‘know how’ in an effort to seek new lucrative niche markets.
“Operating independently, there is always a crossover of views and technologies,” said Jens, elaborating, “For example, Meiser operate as a dyehouse facility to undertake dyeing and coating for Nopma”
“Both companies work side-by-side sharing knowledge in use and handling of chemicals and equipment.”
Modern fabrics
Meiser work with a wide range of modern fabrics and blends, including polyamide, polyester, cotton, micro model and elastane; including frequent mixes of up to four different yarns together with elastane.
“As a service company we must deliver to the highest quality and on time, all based on customer demand,” said Jens.
Customers are generally from around the Albstadt region in Southern Germany, close to the renown scenic Schwarzwald (Black Forest) area, but also include Italy, Austria and Eastern Europe.
“Frequently, the first notification of batch size we get from the customer is on arrival. One day, for example, it could be 50 kg and perhaps 120 kg the next and then 400 kg. The unpredictability of batch sizes however, and the increasing demand for smaller batches, meant that we had to approach the marketplace for a low batch capacity machine to meet our exacting demands. The nature of our business means that many of our machines are developed or produced by us based on our own experience.For this new dyeing machine, even though we have experience with Thies – having a soft-TRD and a more recent roto-stream, purchased in 2001, I have to admit I felt that Thies would not be able to help. We felt certain that it would not be possible to work with a company so successful and as large as Thies explaining our special requirements. Nevertheless we were pleasantly surprised and very impressed.”
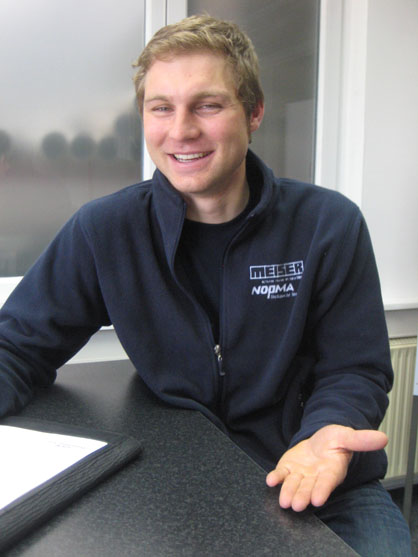
Close collaboration
“Once we had expressed interest in a 4-chamber unit, the opportunity arose to offer our ‘know-how’ in such a dyeing unit.”
Thies’s design team, liaising with Meiser, were able to accept the recommendations throughout the trials of the prototype, including a series of design changes.
These included, for example, the instrument inspection system ‘wash control’ inside the chamber allowing constant monitoring colour measurement throughout the dyeing process, culminating in clear water at the end of the washing cycle.
“Whilst the low liquor ratio is important in respect of utilising costs and energy savings, it was not our principal factor in ordering the new 4-chamber iMaster H2O – quality is always vital, even if it means increased utility costs.”
According to Jens, transportation of the fabrics, particularly those containing elastane, inside the chamber remained absolutely paramount in its demands to achieve the highest shrinkage tolerance.
The new system features a new winch design inside the Kier operating at speeds of up to 500 m/min.
Featuring individual drives, the winch is frequency controlled and features a low rope lifting height to ensure minimum fabric tension. It also offers reduced maintenance, easy handling, lower spare parts costs and is ‘completely’ interchangeable unit.
Flexibility was also an important factor, with the ability according to Jens, to constantly be able to change the design capacity of each chamber.
“With a 100 kg/chamber designed capacity we have been able to produce up to 420 kg to as low as 80 kg utilising all four chambers.”
Meiser was also able to specify its Barco Sedo plc system to ensure complete 100% colour reproducibility between batches with a central control console monitoring the process at all stages.
iMaster H2O
The new iMaster H2O dyeing machine has been designed for fabrics and knitted goods and offers ultra-low dye liquor levels with ratios as low as 1:3.7 for cottons.
The new unit is based on 40 years' experience with this technology and is specifically engineered to ensure that textiles plant are able to adhere to the most stringent of international and local environmental protection regulations.
There is an adjustable iJ-box, making the machine suitable for light to heavy fabrics as well as full and reduced loads. Minimal rope lifting results in better shrinkage control and less rope curling for elastic fabrics such as cotton and Lycra. Running properties cover the range of 90 to 500 m/min, and the dyeing, bleaching and rinsing is carried out with extremely low nozzle pressure, thus giving excellent fabric surface.
Nopma Technical Textiles
The technical textiles company, Nopma, introduced by Jens father before his retirement, has today started to outpace the growth of Meiser, providing a wide range of technical textile finishes.
These can include Nopma anti-slip, a wide variety of gluings, abrasive treatments and temperature controlled fabrics and coatings for both woven and non-woven textiles. Capitalising on the new iMaster H2O dyeing unit, Nopma is able to dye its knitted polyester fabrics for end products such as anti-slip materials for the trunk of Mercedes Series X204 and SLK automobiles.