ITMA-Asia + CITME-2014
2014-06-16
VDMA: German Technology combats pollution
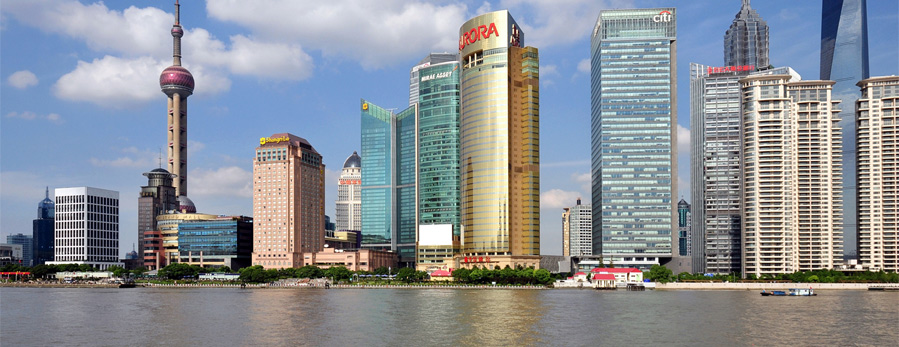
German technology can play a major role in Chinese efforts to make the environment cleaner and to increase the energy efficiency of the textile industry. On occasion of a guided tour initiated by the German VDMA Textile Machinery Association at ITMA ASIA + CITME in Shanghai, high representatives from Chinese authorities and associations and the German General Consul in Shanghai, Dr. Wolfgang Röhr could convince themselves of the energy saving equivalents enabled by German textile machinery.
The savings potentials are enormous: The output of two coal power stations every year, the daily output of the Three Gorges Dam power station, the electricity to power 200 million notebooks one day.
In his address to the Chinese trade press, Dr. Röhr said: “Facing the global challenges climate change is imposing, it is of utmost importance to find a way to decouple economic growth and energy demand. The use of energy efficient technology is one of the most promising measures to approach this goal.” Thomas Waldmann, Managing Director of the VDMA Textile Machinery Association added: “Adjusting to volatile energy prices as well as stricter environmental standards provide a challenge for many textile producers. The German exhibitors here in Shanghai provide profound technological answers on how to cut costs by increasing efficiency.”
Energy-efficient Processes From Fibre to the Final Textile Product
VDMA experts examined the energy saving effects over the entire production chain of three textile products: A cotton T-Shirt, a functional T-Shirt and a textile billboard. Major results of this in-depth analysis of German Technology are summarized in a brochure titled “German Technology: Higher Energy Efficiency - Higher Profits”, that can be obtained at the VDMA booth and the booths of numerous VDMA member companies at ITMA ASIA or be downloaded from the websites
http://china.vdma.org (Chinese) or
http://machines-for-textiles.com/blue-competence/stories (English and German).
On theses websites trade professionals can also read the complete three examples that provide detailed information on which technological measures the increase in energy efficiency is realised. The analysis is comparing German technology of model year 2013 with German technology available one decade ago. This energy efficiency campaign of VDMA and its members is embedded in the sustainability initiative Blue Competence.
What have cotton T-shirts to do with power plants?
Cotton T-shirts are part of the basic garment. German technology reduced 28 per cent of energy consumption for the production of jersey fabric during the past ten years. The saving effects – applied to the production of one T-shirt per year for each of the 7 billion inhabitants of the earth – are enormous: If the worldwide production of cotton T-shirts was made completely on German state-of-the-art technology the output of two coal power stations in Beijing with a total gross power of 1000 megawatt could be saved every year.
Functional T-shirt – Energy savings feed 200 million notebooks
The production of functional T-shirts for sports and leisure clearly shows the progress that was made. German technology of model year 2013 consumes 30 per cent less energy than the predecessor machines and components ten years ago. Translated to 125 million functional T-shirts, which are produced per year worldwide, the overall energy saved for the process steps from yarn manufacturing over warp-knitting up to finishing sum up to 23.5 billion watt hours per year. This is the same energy necessary to power 200 million notebooks during one working day. There is one prerequisite only: All T-shirts will have to be produced with German state-of-the-art textile technology. The bigger textile billboards get, the more energy mattersLarge-area advertising at facades and highways represent a young and ever growing sales segment. The warp-knitted fabric used for outdoor advertising of roundabout 400,000 tons produced worldwide throughout one year would be sufficient to transform the overall metropolis of Guangzhou – covering at least 3,442 square kilometres – into a giant textile billboard. If German machinery technology of latest generation was used exclusively for the production of these textile advertising media, enormous energy savings would be possible for each individual process step. They sum up to 26 per cent. This is equivalent to 300 billion watt hours (300 GWh) per year and the daily output of the world’s biggest hydroelectric power station at the Three Gorges Dam in the Yangtze River.
Lucky draw featuring attractive prizes
Until 30th June 2014, textile manufacturers have the chance to prove their know-how in energy efficiency in a competition featuring attractive prizes. The questionnaire can be answered and sent via internet at
http://china.vdma.org (Chinese) or
http://machines-for-textiles.com/blue-competence (English).
German technology on more than 7,400 square meters
About 115 German exhibitors are on hand at ITMA ASIA + CITME 2014, occupying more than 7,400 square metres of booked space. Measured by square meters, Germany is the biggest foreign exhibiting nation at the major fair for the Asian market. All renowned German manufacturers are present. The German exhibitors cover almost all different machinery chapters with a strong focus on spinning, finishing, knitting and warp knitting, nonwovens as well as weaving technology. For visitors it will be easy and convenient to find and visit German exhibitors as most of them will use the "German Technology" logo. Furthermore, VDMA has initiated German sector groups in hall E1 (weaving), E6 (finishing) and W1 (spinning).
The first point of contact for trade professionals interested in German technology will be the VDMA information booth in the Association Village Tent: Booth T1A01. The tent will be located in the open air area between the E and W halls.
In his address to the Chinese trade press, Dr. Röhr said: “Facing the global challenges climate change is imposing, it is of utmost importance to find a way to decouple economic growth and energy demand. The use of energy efficient technology is one of the most promising measures to approach this goal.” Thomas Waldmann, Managing Director of the VDMA Textile Machinery Association added: “Adjusting to volatile energy prices as well as stricter environmental standards provide a challenge for many textile producers. The German exhibitors here in Shanghai provide profound technological answers on how to cut costs by increasing efficiency.”
Energy-efficient Processes From Fibre to the Final Textile Product
VDMA experts examined the energy saving effects over the entire production chain of three textile products: A cotton T-Shirt, a functional T-Shirt and a textile billboard. Major results of this in-depth analysis of German Technology are summarized in a brochure titled “German Technology: Higher Energy Efficiency - Higher Profits”, that can be obtained at the VDMA booth and the booths of numerous VDMA member companies at ITMA ASIA or be downloaded from the websites
http://china.vdma.org (Chinese) or
http://machines-for-textiles.com/blue-competence/stories (English and German).
On theses websites trade professionals can also read the complete three examples that provide detailed information on which technological measures the increase in energy efficiency is realised. The analysis is comparing German technology of model year 2013 with German technology available one decade ago. This energy efficiency campaign of VDMA and its members is embedded in the sustainability initiative Blue Competence.
What have cotton T-shirts to do with power plants?
Cotton T-shirts are part of the basic garment. German technology reduced 28 per cent of energy consumption for the production of jersey fabric during the past ten years. The saving effects – applied to the production of one T-shirt per year for each of the 7 billion inhabitants of the earth – are enormous: If the worldwide production of cotton T-shirts was made completely on German state-of-the-art technology the output of two coal power stations in Beijing with a total gross power of 1000 megawatt could be saved every year.
Functional T-shirt – Energy savings feed 200 million notebooks
The production of functional T-shirts for sports and leisure clearly shows the progress that was made. German technology of model year 2013 consumes 30 per cent less energy than the predecessor machines and components ten years ago. Translated to 125 million functional T-shirts, which are produced per year worldwide, the overall energy saved for the process steps from yarn manufacturing over warp-knitting up to finishing sum up to 23.5 billion watt hours per year. This is the same energy necessary to power 200 million notebooks during one working day. There is one prerequisite only: All T-shirts will have to be produced with German state-of-the-art textile technology. The bigger textile billboards get, the more energy mattersLarge-area advertising at facades and highways represent a young and ever growing sales segment. The warp-knitted fabric used for outdoor advertising of roundabout 400,000 tons produced worldwide throughout one year would be sufficient to transform the overall metropolis of Guangzhou – covering at least 3,442 square kilometres – into a giant textile billboard. If German machinery technology of latest generation was used exclusively for the production of these textile advertising media, enormous energy savings would be possible for each individual process step. They sum up to 26 per cent. This is equivalent to 300 billion watt hours (300 GWh) per year and the daily output of the world’s biggest hydroelectric power station at the Three Gorges Dam in the Yangtze River.
Lucky draw featuring attractive prizes
Until 30th June 2014, textile manufacturers have the chance to prove their know-how in energy efficiency in a competition featuring attractive prizes. The questionnaire can be answered and sent via internet at
http://china.vdma.org (Chinese) or
http://machines-for-textiles.com/blue-competence (English).
German technology on more than 7,400 square meters
About 115 German exhibitors are on hand at ITMA ASIA + CITME 2014, occupying more than 7,400 square metres of booked space. Measured by square meters, Germany is the biggest foreign exhibiting nation at the major fair for the Asian market. All renowned German manufacturers are present. The German exhibitors cover almost all different machinery chapters with a strong focus on spinning, finishing, knitting and warp knitting, nonwovens as well as weaving technology. For visitors it will be easy and convenient to find and visit German exhibitors as most of them will use the "German Technology" logo. Furthermore, VDMA has initiated German sector groups in hall E1 (weaving), E6 (finishing) and W1 (spinning).
The first point of contact for trade professionals interested in German technology will be the VDMA information booth in the Association Village Tent: Booth T1A01. The tent will be located in the open air area between the E and W halls.
Related News
Latest News ITMA-Asia + CITME-2014
2014-08-13
More News from VDMA Fachverband Textilmaschinen
2024-09-23
2024-08-15
2024-05-23