Yarn & Fiber
Solvay launches Technyl® 4earth® to reduce the environmental footprint of high performance materials
Such pioneering innovation is born from the Move 4earth® project supported by the European Commission (LIFE+ program) and recently awarded the Pierre Potier Prize for sustainable and eco-responsible developments. Industrialized in Poland, this patented process transforms stable sources of post-industrial or end-of-life technical textiles, such as automotive airbags, into prime quality engineering plastics. This unique technology offers novel eco-friendly products with similar performance when compared to our traditional Technyl®.
“Technyl® 4earth® significantly reduces the environmental impact of polyamide parts to a level that has never been reached before,” adds Richard Bourdon, Move 4earth® Project Director. “Solvay’s initial cradle-to-gate assessment shows outstanding results: carbon footprint reduced by a quarter; consumption of non-renewable resources divided by two; and water use decreased by over two-thirds compared to traditional compounds!”
Officially launched at K2016 in Düsseldorf, Solvay is already developing a number of applications using Technyl® 4earth® with major players in automotive and consumer goods markets.
Solvay also supports customers with a complete array of technical services designed to speed the time to market of new applications, from advanced material characterization to application validation. This offering includes 3D printing of PA6-based functional prototypes in Sinterline® PA6 powders, predictive simulation with MMI® Technyl® Design as well as part testing at fully equipped APT® Technyl® Validation centers.
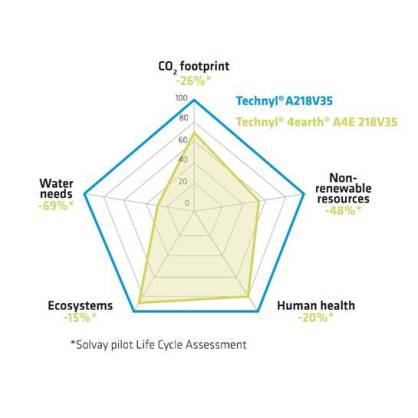
Pic: The cradle-to-gate environmental footprint of Technyl® 4earth® is significantly reduced vs. prime Technyl® PA6.6 (Graphic courtesy of Solvay)