Techtextil 2017
ITA presents four innovations at Techtextil
1. PolyTube
Carbon Fibres are used as reinforcement in the automotive and aerospace sector. EoL components and production waste fibres can be recycled to rCF (recycled carbon fibres). rCF may then be used to produce new components. An appropriate process is the fabrication of semi-finished nonwovens for further processing.
The exhibit is a GFP-tube with layers of rCF-nonwoven. The aim is the electrical functionalization of GFP-tubes using the electrical conductivity of rCF-fibres. It is thus possible to discharge static charges, to realise a cost-efficient heating of the tube and to detect defects within the pipe’s wall. For further information please contact christian.moebitz@ita.rwth-aachen.de.

Picture 1: PolyTube, Glass fibre reinforced plastic tube with rCF on the interior side, source: ITA
2. ScaffBag – sensor based airbag for protection from damage induced by falling
The personal protective equipment consists of an airbag system combined with a sensor-based inflation. The airbag is an OPW (one-piece-woven) structure with complex geometry. An important feature is the seamless textile structure, but with higher tensile strength and higher security standard than conventional products.
In addition, a purchase incentive can be created by "safety made in Germany". Optionally new standards for safety at work (in cooperation with professional association BG Bau) can be achieved. For further information please contact gesine.koeppe@ita.rwth-aachen.de.
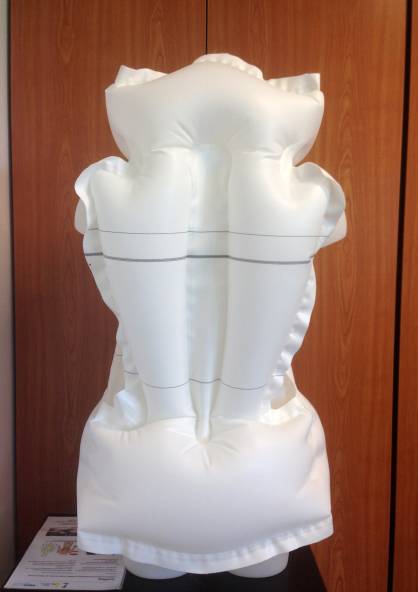
The production of tailored non-crimp fabrics (T-NCF) has a huge potential as a key technology for the fibre composite industry due to its high flexibility and low process costs.
The state-of-the-art production of structural fibre composite components in the automotive and aerospace industry is the production of non-crimp fabrics as rolled goods. They are tailored in accordance with the component geometry, the required component properties and mechanical and assembled via preforming.
Manual labour and a large amount of cutting waste account for 50 % of the process and component costs.
The T-NCF process integrates the presently cost-intensive preforming process within the non-crimp fabrics production and thereby leads to high cost savings. The high cost savings make the T-NCF technology interesting for large serial production e.g. in the automotive or aerospace industry.
On completion of the validation phase, the technology can be used in industrial scale within 3 or 4 years. For further information please contact Wilko.Happach@ita.rwth-aachen.de.
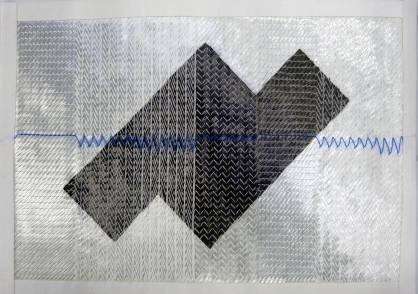
Picture 3: Tailored Non-crimp Fabrics, source: ITA
4. Hybrid-nonwoven reinforced organo sheet
The demonstrator shows a PA6-sheet that is reinforced with carbon staple fibres. Novelty of this material is the application of a combined nonwoven structure, which allows the individual design of nonwoven reinforcement structures. The demonstrator shows different possible reinforcement-structures by different surface materials. This product is the first of its kind worldwide. Staple fibre nonwovens can be combined to design a 3D-reinforcement-structure for composites.
Therefore, this development leads to the development of a novel material class. This material will be applied as functional surface material in lightweight construction. Besides good optic and haptic, the application of heat generation and EM-shielding for transportation and design applications is expected. For further information please contact frederick.cloppenburg@ita.rwth-aachen.de.
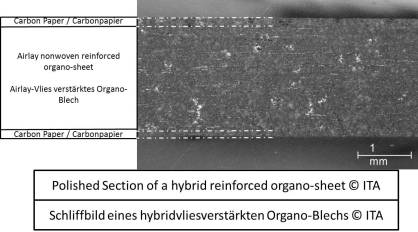
Picture 4: Polished section of a hybrid reinforced Organo-sheet, source: ITA