ITM 2024
Mayer & Cie. presents new machine types and efficient solutions in Istanbul
"We are convinced that the ITM show will drive the textile machinery sector forward by providing a platform for industry leaders to network, share ideas and showcase progress," says Benjamin Mayer, Managing Partner of Mayer & Cie. "This can stimulate innovation, kick-start investment and ultimately drive the sector forward after a period of stagnation."
Making the tried and tested even better: Relanit 3.2 HS II
The Relanit 3.2 HS is by far Mayer & Cie's best-selling machine. Customers appreciate its productivity, especially in connection with elastomeric plating. The mechanical single jersey model processes a wide range of yarns and qualities extremely reliably. The machine also impresses with its energy efficiency: the energy consumption of the Relanit 3.2 HS is up to 30 percent lower than that of a circular knitting machine with conventional technology.
New yarn guide for the Relanit 3.2 HS II
In its updated form, the Relanit 3.2 HS II is equipped with a new thread guide, which makes threading of the elastic thread much easier.
Models already on the market can be upgraded to be equipped with the new yarn guide.
Cooperation with Groz-Beckert
Another innovation the Relanit 3.2 HS II is equipped with are improved needles and sinkers: The needle with serrated edge and predetermined breaking point, developed jointly with Groz-Beckert, prevents it from breaking uncontrollably under high load or a defective needle tongue and, in the worst case, from breaking needle butts – which in turn requires more complex intervention by the knitter.
Axel Brünner, Senior Product Manager at Mayer & Cie.: "With this improvement, we are reducing downtime for the Relanit 3.2 HS II."
The new sinker was also developed jointly with Groz-Beckert. With that, the Relanit 3.2 HS runs more smoothly, more quietly and with less wear and tear. At higher speeds the thread tension increases less sharply too, thereby reducing the likelihood of faults in the fabric even with exacting qualities like sustainable cotton. The new sinker also makes setting the lower swing curve unnecessary, which in turn makes gauge changes simpler.
SF4-3.2 III for lightweight 3-thread fleece fabrics
With its SF4-3.2 III, Mayer & Cie. is addressing a trend in the clothing industry that has been underlined by Turkish customers in particular: Lightweight elastic three-thread fleece fabrics in both pure cotton and cotton blends are very much in demand. “In this new machine,” Axel Brünner, senior product manager at Mayer & Cie., explains, “we combine our tried and trusted S4 3.2 II and components from our MBF 3.2 such as the stitch formation”.
One of its most impressive features is its plating performance. The exhibitors demonstrated it most impressively by means of the black ground yarn that could not be seen on the front of the fabric. That testified to the quality of the plating – with the result that single dying is sufficient.
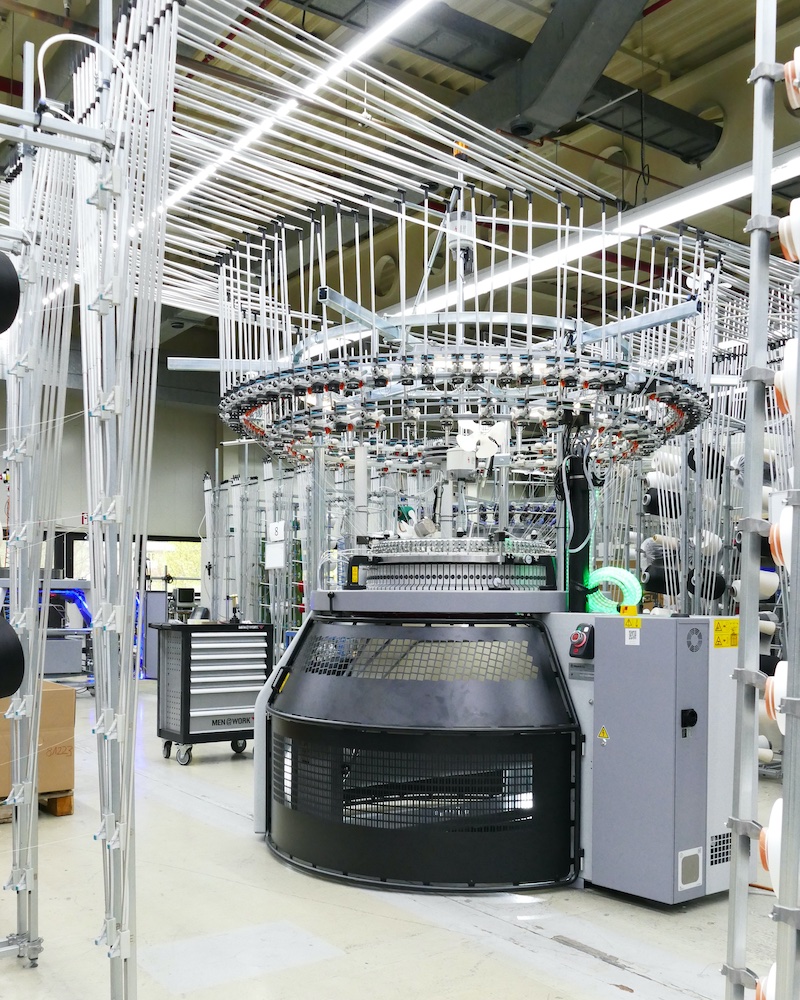
New Control 5.0 machine control system
Both machines are equipped with the new Control 5.0 machine control system. It is available in two versions. In the standard version, it comes as SmartControl, which means that a so-called Smart Knob is attached to each machine foot. From there, all the functions that the machine operator needs for his work are available. More in-depth settings, such as those the knitting mill manager wants to make, are only possible from a mobile device. Any number of Mayer & Cie. machines can be operated from this machine at the same time. In the ClassicControl version, Control 5.0 is mounted as a monitor at the familiar location on the machine. As before, this can only be controlled from this point.
All machines built from 2001 onwards can be converted, and selected new machines will be equipped with the new generation of machine control systems from 2024.
knithawk: for knitting defects detected at once
Circular knitting machines such as the Relanit 3.2 HS II are extremely productive: they rotate up to 50 times a minute and produce up to 40 kilograms of fabric per hour. If a knitting error occurs – for example due to external influences in the yarn – many metres of unusable knitted fabric may run off the machine, because a fabric inspection has often only been carried out after the knitting process or even after the finishing.
knithawk, a tool for optical defect detection, starts earlier – namely in the single jersey machine, directly at the knitting point. knithawk is compact: the camera unit, which "scans" the knitted fabric using infrared light, is quickly installed. If knithawk detects a serious or recurring error, the machine is stopped. The tool also creates an error log.
In this way, knithawk can prevent knitting errors from spreading through many meters of knitted fabric. Resources such as water, natural fibres, polyester and energy are not used in vain thanks to knithawk.
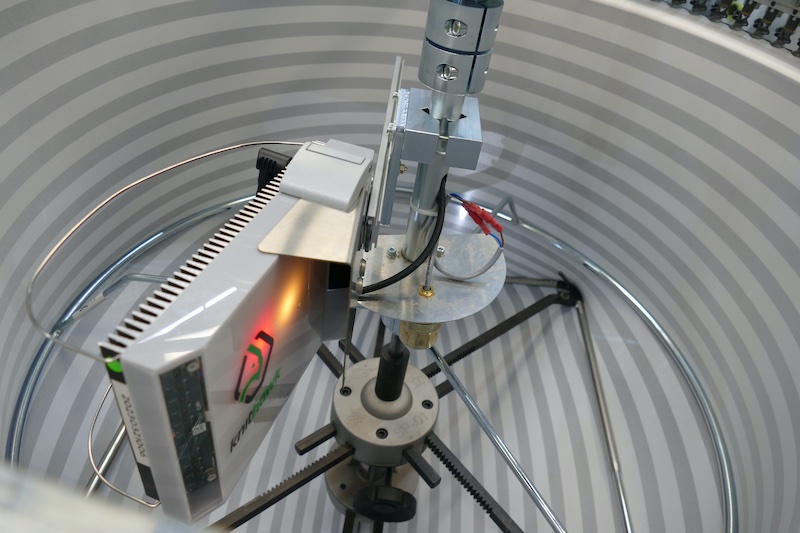
Machine-specific upgrade kits
With its upgrade kits, Mayer & Cie. brings technological innovations to existing machines. These range from machine-specific upgrades, such as the Performance Kit for existing Relanit 3.2 models or the "Speed Boosting Kit" for the OVJA 1.6 EE, to the Control 5.0 Upgrade Kit.
Senso Blue RS
Also available for retrofitting and as an option for new machines is the new, machine-integrated Senso Blue RS lubrication system. The oil is applied in the optimal amount and with pinpoint accuracy to needles such as circuit boards. The oil application is speed-dependent. The used oil is collected, filtered several times and then fed back into the system. The lubricator system is controlled by the machine control system.
When it comes to oil consumption – and thus sustainability – the oiler can make a real difference: The optimal oil application leads to a reduced oil consumption that is around 20 percent lower than that of a conventional oiler. In addition, the recycling rate of used oil reaches up to 40 percent.
Conversion kits for more flexibility
In addition to the upgrade kits, Mayer & Cie. offers conversion kits for popular machine types. Currently, two are available for single jersey machines: The MV4 3.2 II, popular in the underwear sector, for example, can be converted into the MBF 3.2 binding thread lining machine. A second conversion kit turns an S4-3.2 II into an SF4-3.2 III – and vice versa.
"Our conversion kits also serve the goal of making existing machines even more valuable and valuable," says Benjamin Mayer. "For a low price compared to the purchase of a new machine, the customer gets an additional machine model with all its possibilities, so to speak."
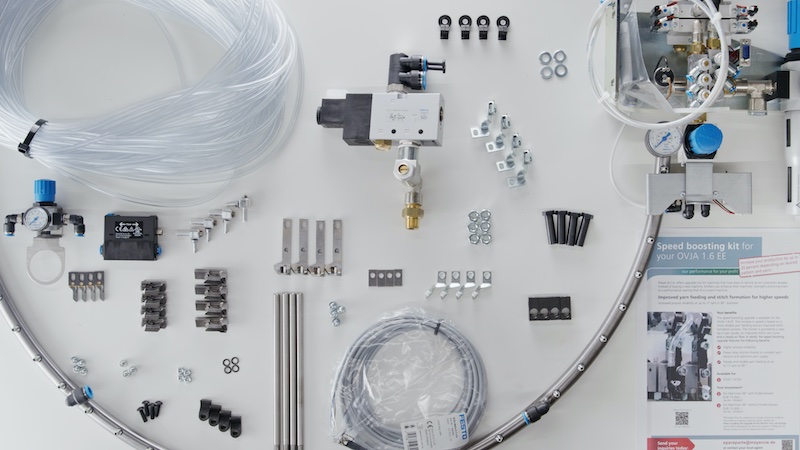