Research & Development
Next-generation sustainable carbon fibers: versatile, high-performance and economical
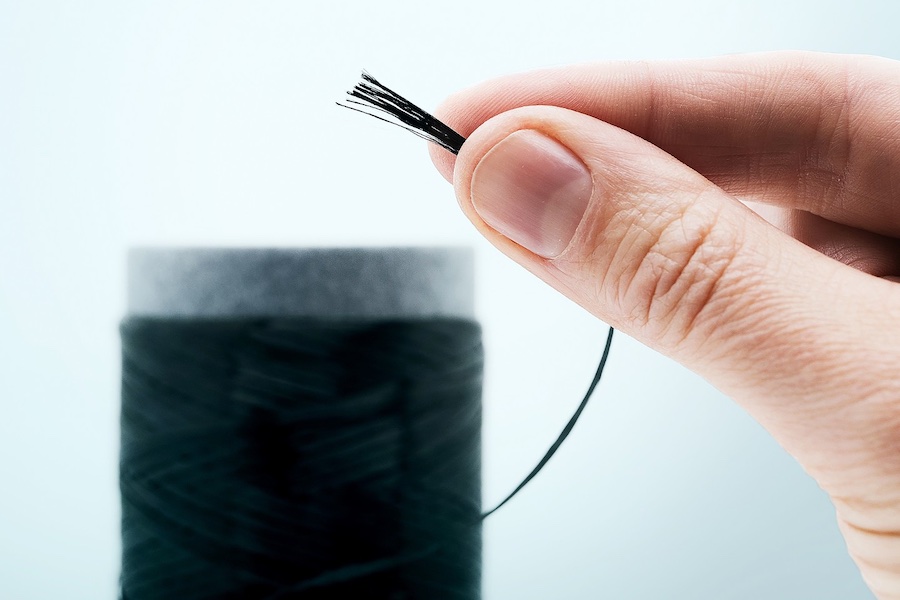
These fibers combine structural diversity, high electrical, thermal and mechanical performance with sustainability. The project is part of the Carbon Lab Factory Lausitz and is funded by the German Federal Ministry for Economic Affairs and Energy. It is intensively supported by the Wirtschaftsregion Lausitz GmbH.
More than lightweight construction: carbon fibers for alternative high-tech applications
Traditional carbon fibers, such as those used in lightweight construction, are usually made from the petroleum-based polymer polyacrylonitrile (PAN). Their production is complex, energy- and resource-intensive, and generates large quantities of toxic by-products. Pitch-based carbon fibers, another petroleum-derived type with excellent electrical and thermal properties, are highly technically demanding and costly to produce.
The Fraunhofer IAP is addressing these challenges with a new generation of high-performance carbon fibers – bio-based and sustainable. They combine structural variability with customizable properties and an attractive environmental and economic profile. Their applications go far beyond lightweight construction for aerospace, defense, wind energy or medicine: as a component in batteries and fuel cells, they can serve as electrical and thermal conductive, chemically stable fabrics. They are also ideally suited for shielding sensitive electronics.
High variability through spinning processes and additives
The innovative approach of the Fraunhofer IAP uses cellulose as a renewable raw material for precursors – the starting material for carbon fibers. Precursor fibers can be spun into continuous filaments using established industrial spinning technologies such as the viscose or Lyocell processes, as well as alternative shaping methods. Additives such as lignin, which like cellulose is derived from wood, can be incorporated directly into the spinning solution, significantly boosting the carbon yield during subsequent conversion to carbon fibers.
A key advantage of cellulose is that the structure of the precursor fibers – and thus the resulting carbon fibers – can be precisely controlled through the selected spinning process and parameters. This results in various degrees of orientation and crystallinity, as well as fiber cross-sections – for example, round, oval or lobulated. The latter one offers a particularly high specific surface area and is therefore suitable for use in conductive, porous structures for permeable electrodes in redox flow batteries or gas diffusion layers in fuel cells.
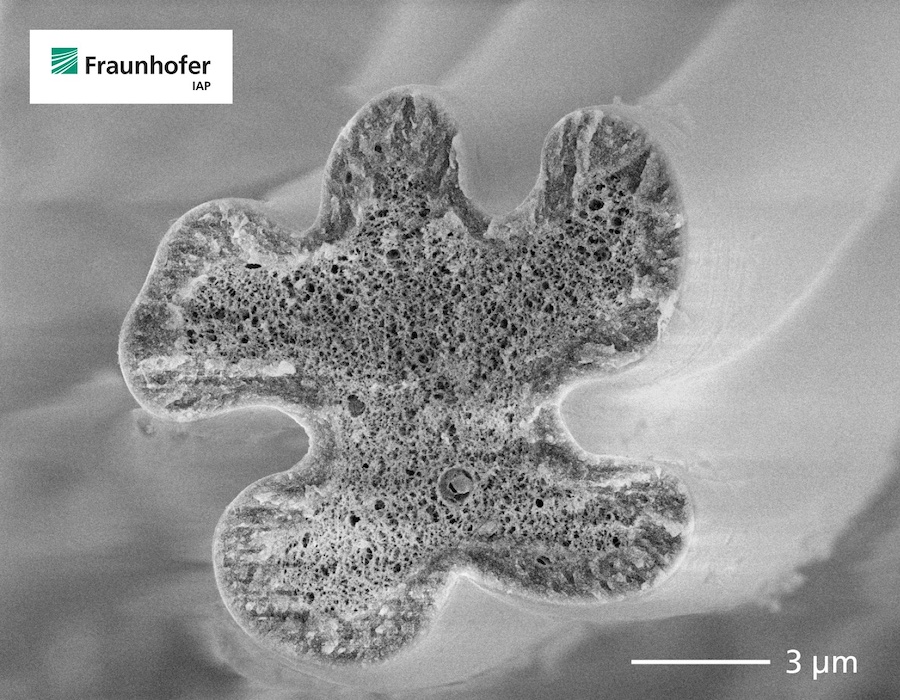
Catalysis makes bio-based carbon fibers competitive
The endless spun cellulose fibers then pass through an aqueous bath containing functional additives or catalysts. This step activates the material for the subsequent thermal conversion into carbon fibers. Here, the cellulose fiber has a special advantage: it behaves like a sponge, efficiently absorbing the additives from the bath. The system of catalysts and additives developed by Fraunhofer IAP lowers the carbonization temperature by more than 1,000 °C, accelerates the process, and increases the yield from 15 to 45 percent by weight.
By specifically optimizing process parameters – such as temperature, residence time or mechanical stretching – during carbonization, fiber diameters well below four micrometers can be achieved. This is particularly relevant for fuel cells. By comparison: commercial fibers typically measure around seven micrometers in diameter.
Customized high performance – mechanical, electrical, thermal
The combination of spinning, activation and carbonization technologies allows the development of customized fiber types for a wide range of applications. Dr. Jens Erdmann, expert for bio-based carbon fibers at the Fraunhofer IAP, emphasizes: "Our carbon fibers combine high technical performance with sustainability: their mechanical properties are comparable to those of petroleum-based high-modulus PAN carbon fibers – in other words, to those of high-performance carbon fibers. They also show electrical and thermal properties similar to pitch-based fibers."
Carbon Lab Factory Lausitz: a bridge to industrial scaling
Pilot-scale trials at the Fraunhofer IAP demonstrate the great potential of this technology – which is now to be scaled up as part of the "Carbon Lab Factory Lausitz" initiative. The new infrastructure will cover the entire value chain – from raw material via carbon fiber to technical components – in Germany. The initiative was launched jointly with TU Chemnitz and Institute of Lightweight Design and Value-added Management of the BTU Cottbus-Senftenberg and is a cross-federal state project between Saxony and Brandenburg. It supports the development of a globally unique research infrastructure for carbon fibers and thus the structural transformation of the Lausitz region.
Sustainability meets high performance – a growing demand
"We clearly see that interest in sustainable materials is steadily increasing," says Erdmann. "But ecological advantages alone are not enough to succeed on the market – economic performance is also crucial. That’s exactly where we come in: we’ve succeeded in combining ecological responsibility with technical performance and cost-efficiency. The ability to tailor and flexibly adapt the properties of our fibers opens up new fields of application and clear competitive advantages – a decisive step toward economic viability."