Dyeing, Drying, Finishing
The Monforts technology behind some beautiful curves
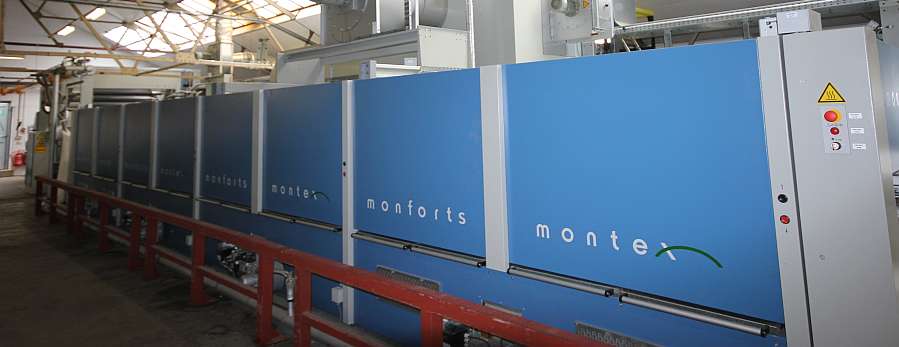
“The company probably never looked back from that time,” said Production Director Kevin McAndrew, who oversaw the initial implementation of the dyeing and finishing department and has run it ever since.
“It’s probably the best thing we ever did and was simply a matter of wanting to be in greater control of our business. Before we had our own dyeing and finishing operation we were sending back four out of every ten of our commission dyed batches.”
Today, the largest market for Simplex fine gauge stretch and non-stretch (rigid) fabrics is in lingerie and intimate apparel, with a specialisation in bra cups, for key brand customers including Fantasie, Freya, Playtex and Wacoal. Simplex fabrics are generally valued for their unique characteristics and in bras to gently envelope a woman’s curves, providing shape and support, with an attractive, smooth, voluminous handle.
In addition to the ‘Simplex’ fabric production, 40 gauge tricot and 28 gg raschel power fabrics are supplied world-wide from the Chilwell factory.
The company also knits satins and charmeuse, tulles and mesh, a range of lightweight, soft stretch locknits and high power performance fabrics, as well as those incorporating branded fibres including Lycra, Coolmax, Coolplus and Novarel.
It can supply various print options including wet and paper prints, digital printing and delustre surfaces. And an extensive range of embossed designs can be applied to any of its 100% polyester fabrics.
Employing 37 people at the Chilwell site, Simplex also supplies to the active sportswear, cosmetic textiles, industrial and medical sectors.
While all of the company’s fabric is knitted in the UK, it also has dyeing and finishing operations in China and Sri Lanka plus further offices in Hong Kong and Colombo, which form part of its extensive and logistics and distribution network.
“The majority of the fabrics knitted here go to Asia. The finished garments however will end up back in European and US stores,” Mr McAndrew observed.
The latest Montex 8000 stenter that has been installed at the Chilwell plant is unique in having two padders in sequence at its entry.
“This was necessary because we don’t have any water extraction and this configuration allows us to squeeze on the first padder and apply finishes on the second in a single pass,” Mr McAndrew explained. The stenter is also unusual in having only four chambers, partly because this is all the company requires to finish the lightweight and delicate fabrics it makes, but also for reasons of limited space within the plant; which is also making it necessary for a new building to be built to accommodate yarn and greige fabric stock. The machine is working to its maximum capability and Mr McAndrew notes a number of new feature benefits over its predecessor.
“The control system is so much easier to operate on the new machines and once we’ve established a quality we can automatically repeat it,” he said. “And as far as service and troubleshooting is concerned, the stenter is now directly linked by modem to Germany and we can make immediate contact with Monforts engineers. Because everything is electronic, it’s much easier to solve any issues that may arise. It’s a vast improvement on what we had before and we’re now very happy with it.”
The new stenter was ordered through local representative Colplan Engineering.
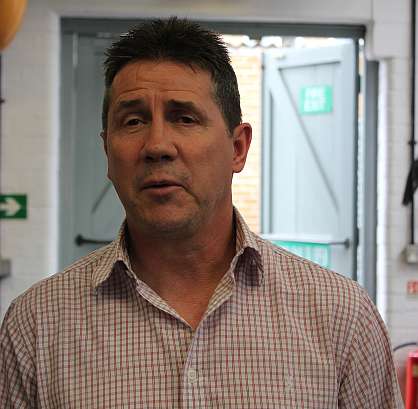
Pic: Production Director Simplex Knitting Company Mr. Kevin McAndrew