Composites
ITA at COMPOSITES EUROPE
At the booth of the Aachen Centre for Integrative Lightweight Production (AZL) in Hall C2, booth A42, current exhibits from the automotive, aviation, wind power and construction sectors will be shown:
1. Fibre-composite pressure vessel
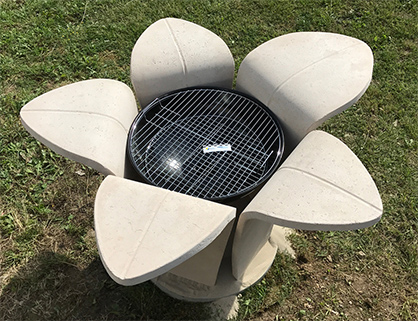
At our booth, we’re showing a fibre-composite pressure vessel made from carbon tow prepreg, produced in the multifilament winding process. Fibre-composite pressure vessels can be used for a variety of applications, including as fuel storage in fuel cell vehicles.
- The vessels are highly pressure resistant, withstanding up to 700 bar
- Because of the high pressure, they can save more fuel
- They are considerably lighter than conventional pressure vessels
- The advantages allow vehicles with carbon pressure vessels to have a much greater range
Another advantage lies in the production method of the pressure vessel which allows for both mass production and a considerably higher production speed compared with the conventional wet winding process:
- The vessel was produced in the multifilament winding process with machines available at the ITA, such as the MFW 48-1200, which is manufactured by the Japanese company Murata Machinery. This machine is able to process up to 48 rovings simultaneously and produces a complete fibre layer in just one production step. This speeds up the production process significantly.
- The cycle time of this multifilament winding process is up to 50 times lower and is therefore predestined for mass production.
Further, the non-crimped fibre layer of the rovings on the liner features excellent mechanical properties. When using the conventional winding process, the rovings create crossing points, worsening the mechanical properties of the vessel. For further information, please contact pia.muench@ita.rwth-aachen.de .
2. Automotive door panel made from biodegradable materials
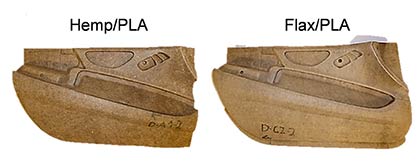
The automobile’s door panel is completely produced out of biodegradable materials, such as flax, hemp, and polylactide (PLA). Unlike earlier models, which were manufactured using polypropylene as the thermoplastic matrix, the ‘new’ materials are completely biodegradable. The System4Green Project, which was completed in December 2016 together with the German Federation of Industrial Research Associations (AiF), the application of natural and PLA fibres was optimised with bio based/biodegradable additives to fulfil the standards of the automotive industry. Original Equipment Manufacturers, TIER 1 (Composite manufacturers) and TIER 2 (Nonwoven producers) suppliers are able to reach the required recycling quotas, as the materials are fully biodegradable and are therefore completely recyclable, without incineration.
Another advantage: The production process with flax, hemp, and PLA is – at current price levels – cheaper than using conventional materials. For further information, please contact frederik.cloppenburg@ita.rwth-aachen.de
3. Concrete mold for the production of longboards made from carbon fibre reinforced polymers (CFRP)
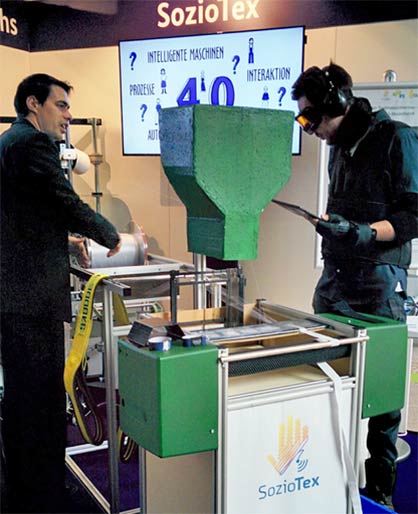
The exhibit at ITA’s booth shows the prototype mold made out of textile reinforced concrete, used to manufacture longboards made from carbon fibre reinforced polymers (CFRP). The prototype was developed in cooperation with the company KMB Keramischer Modell- und Formenbau GmbH, Wesel. The prototype mold is meant to be a replacement for mold made of synthetic materials (Ureol, plate material), aluminum or steel.
Here we use the form for vacuum infusions with epoxide resin and carbon or glass fibres. Molds made out of fibre reinforced concrete for the production of fibre reinforced plastic (FRP) components are not yet on the market. Due to its temperature resistance, a FRP component can be infused and subsequently annealed in the mold. The material and production cost for this concrete mold are significantly lower than conventional molds. New molds do not have to be milled again from the solid or elaborately produced by hand-laminating processes; instead, after the production of the master mold, they can be reproduced easily and cheaply. For the producers of fibre composite materials, which include the automotive industry and its suppliers, there are substantial advantages:
- forming costs are reduced considerably as the molds can be made cheaply from a single prototype
- Annealing of the parts directly in the mold.
First parts are already being manufactured successfully and show the great potential for concrete forms in the production of fibre composite materials. For further information, please contact info@bleckmann-kmb.de or sven.schoefer@ita.rwth-aachen.de .